CASE
KIWI and Meny supermarkets
Cleaner air and energy savings
The installations were carried out in a Meny supermarket and a KIWI supermarket, where the full implementation of Multisens adaptive ventilation control was combined with high-efficiency electronic filters.
Supermarkets worldwide face intense competition and an increasing need to control costs. With a net profit margin of only 1–3% of revenue, every saving is critical. This, combined with the need to provide customers with a good shopping experience, has placed a strong focus on ventilation in KIWI and MENY supermarkets.
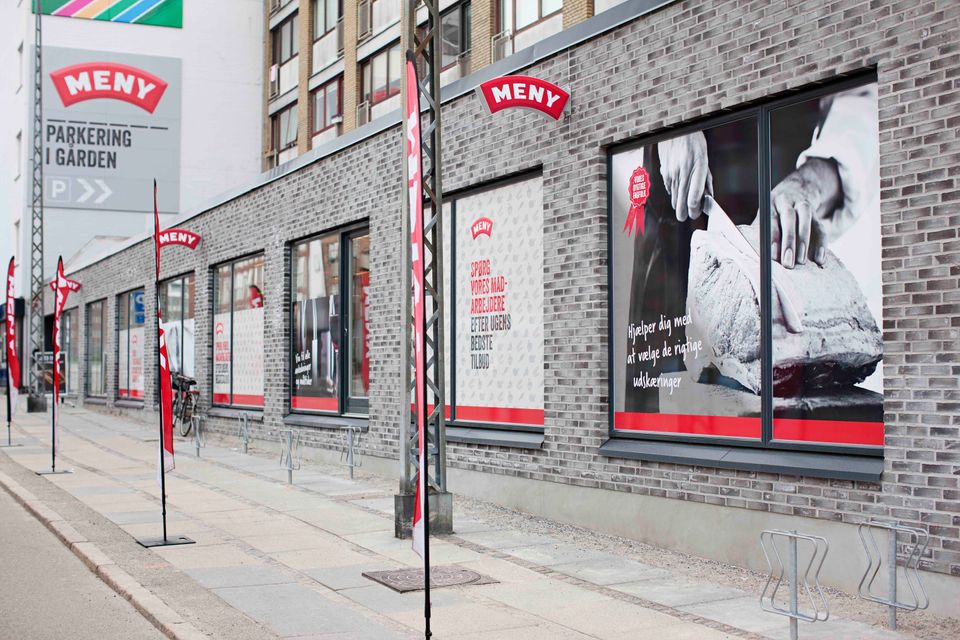
The data collected over the period documents that the supermarkets’ total energy consumption can be reduced by 12–22%. The savings cover energy for heating, cooling, ventilation, as well as kitchen equipment, refrigeration units, and lighting, while at the same time improving air quality and indoor climate control.
The accumulated results have now created a foundation for further implementation among other supermarkets.
Food safety and air quality:
Effective air quality management in supermarkets is not just about energy, It is also fundamental aspect of food safety and comfort.
Implementing advanced filtration, ventilation, and monitoring systems helps protect food from contamination, extend shelf life, and comply with regulatory standards, ultimately ensuring a more comfortable shopping experience for consumers.
Airborne bacteria, mold spores, and viruses can settle on fresh produce, baked goods, and open food displays
High humidity levels encourage mold growth, especially in refrigerated and produce sections
Dust, pollen, and other airborne particles can settle on food surfaces, reducing quality and increasing allergen risk
Supermarkets use cleaning agents, refrigerants, and packaging materials that can release volatile organic compounds (VOCs) into the air
The SQF program emphasizes the importance of air quality monitoring in food storage and retail environments
Poor air quality accelerates oxidation and spoilage, especially in perishable items like fruits and vegetables
Poor air quality and climate control impact the overall shopping experience
Improved air quality with 85% recirculation
During the test period, an average of 85% recirculation was achieved while air quality was carefully measured and managed using the Multisens system. TVOCs were monitored and controlled using PID sensors, along with CO₂, temperature, and humidity sensors.
Special focus was placed on suspended fine particles, which were measured using high-grade ISO 14644-calibrated sensors, counting particles in the size ranges 0.3 µm, 0.5 µm, 1.0 µm, 2.5 µm, and 5.0 µm.
Additionally, the total particle mass below 2.5 µm (PM₂.₅) was measured. Air quality was managed by setting threshold values, ensuring that ventilation was 100% controlled based on Multi-Sense data.
The below data was collected over a busy weekend from February 28, 2025, to March 1, 2025. At no point were the thresholds exceeded. The in-store air was continuously cleaned using ESP filters, maintaining a recirculation rate of 85%. This process effectively kept the concentration of suspended fine particles lower than that of the ambient air before filtration.
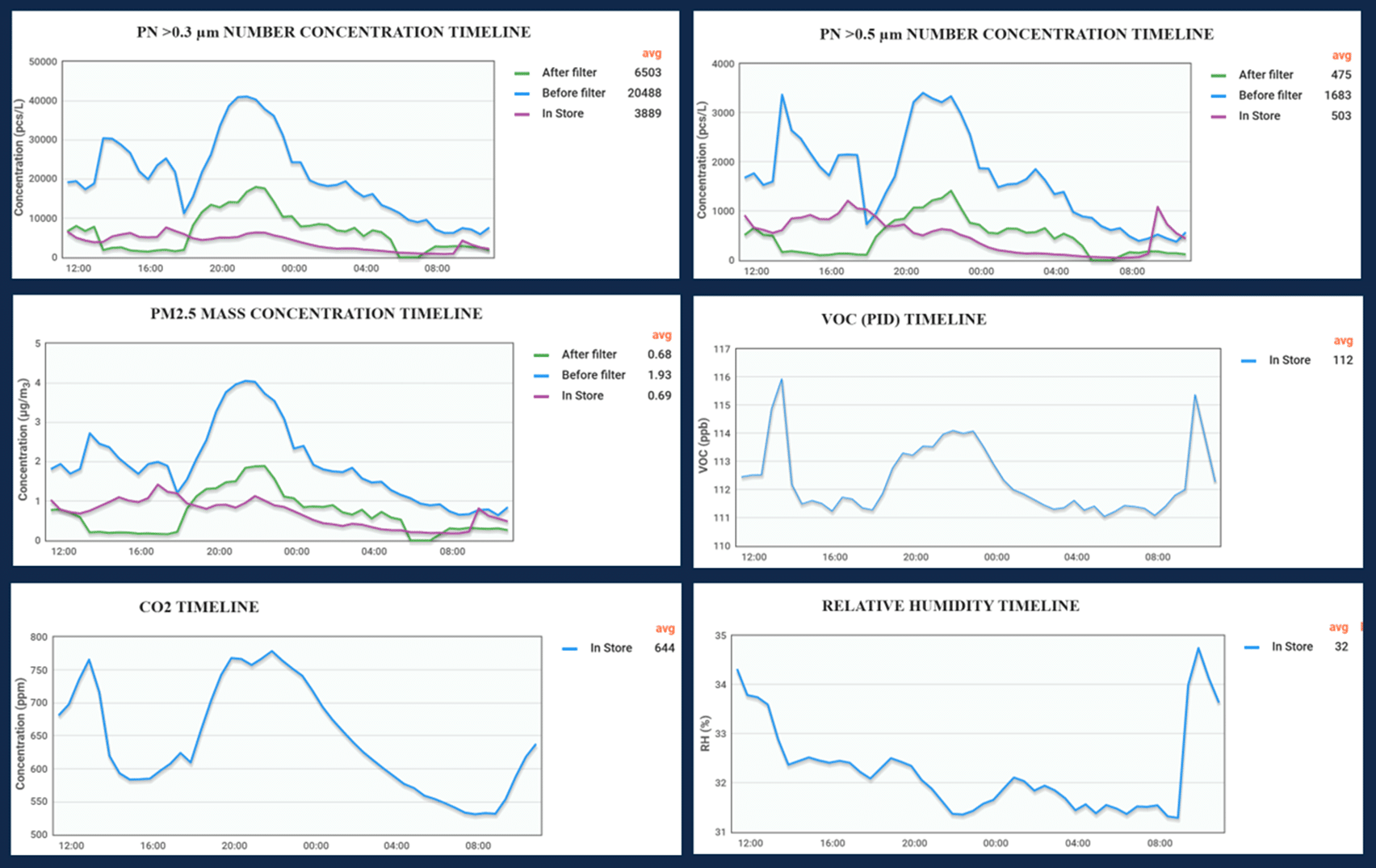